How Can You Measure Operational Efficiency?
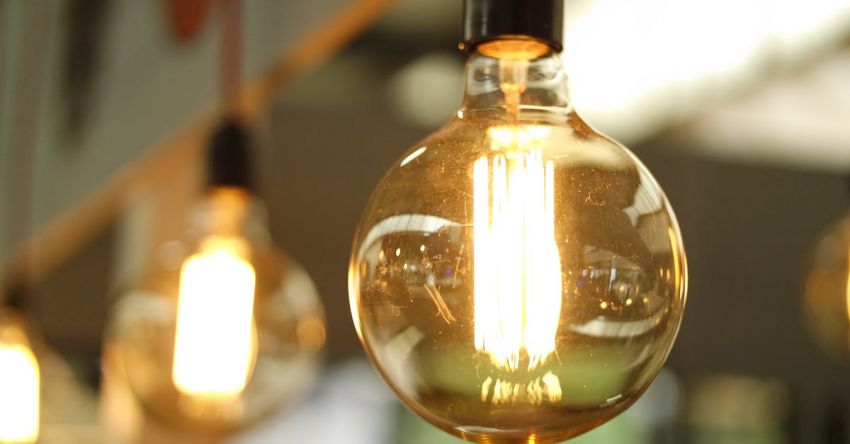
Operational efficiency is a critical aspect of any successful business, as it directly impacts the organization’s ability to maximize output while minimizing input. In today’s competitive business landscape, companies are constantly striving to improve their operational efficiency to stay ahead of the curve. But how can you measure operational efficiency effectively to identify areas for improvement and drive growth? Let’s delve into some key metrics and methods that can help you assess and enhance your operational efficiency.
Key Performance Indicators (KPIs)
One of the most common ways to measure operational efficiency is through the use of Key Performance Indicators or KPIs. KPIs are specific metrics that help organizations track and evaluate their progress towards achieving strategic objectives. When it comes to measuring operational efficiency, there are several KPIs that can provide valuable insights into the effectiveness of your operations.
Some common operational efficiency KPIs include:
– Overall Equipment Effectiveness (OEE): OEE is a metric that measures the performance of equipment in terms of availability, performance, and quality. By calculating OEE, you can identify areas where equipment downtime or inefficiencies are impacting your operational efficiency.
– Cycle Time: Cycle time refers to the total time it takes to complete a process or task. By tracking cycle times for different operational activities, you can pinpoint bottlenecks and inefficiencies that are slowing down your operations.
– Cost per Unit: Cost per unit is a metric that helps you understand the cost of producing each unit of a product or service. By monitoring cost per unit, you can identify opportunities to reduce costs and improve operational efficiency.
– Employee Productivity: Employee productivity measures the output generated by each employee within a specific time frame. By tracking employee productivity, you can assess the efficiency of your workforce and identify areas where additional training or resources may be needed.
Benchmarking
Another effective method for measuring operational efficiency is through benchmarking. Benchmarking involves comparing your organization’s performance against industry standards or best practices to identify areas for improvement. By benchmarking your operational processes against top-performing companies in your industry, you can gain valuable insights into where your operations stand and what steps you can take to enhance efficiency.
Process Mapping
Process mapping is a visual tool that allows you to outline and analyze your operational processes step by step. By mapping out your processes, you can identify redundancies, inefficiencies, and areas for improvement. Process mapping can help you streamline your operations, reduce waste, and enhance overall efficiency.
Technology Adoption
In today’s digital age, technology plays a crucial role in driving operational efficiency. By adopting advanced technologies such as automation, data analytics, and Enterprise Resource Planning (ERP) systems, you can streamline your operations, improve decision-making, and enhance productivity. Leveraging technology can help you automate repetitive tasks, reduce errors, and optimize resource allocation, leading to significant improvements in operational efficiency.
Continuous Improvement
Continuous improvement is a fundamental principle of operational efficiency. By fostering a culture of continuous improvement within your organization, you can encourage employees to identify and implement changes that enhance efficiency. Whether through Kaizen events, Lean Six Sigma methodologies, or other improvement initiatives, continuous improvement can help you drive operational excellence and stay ahead of the competition.
In conclusion,
Measuring operational efficiency is crucial for identifying areas of improvement and driving business growth. By leveraging KPIs, benchmarking, process mapping, technology adoption, and continuous improvement practices, you can assess your operational performance, optimize your processes, and enhance efficiency across your organization. By focusing on these key strategies, you can position your business for long-term success in today’s highly competitive market.