What Are the Best Practices for Inventory Management?
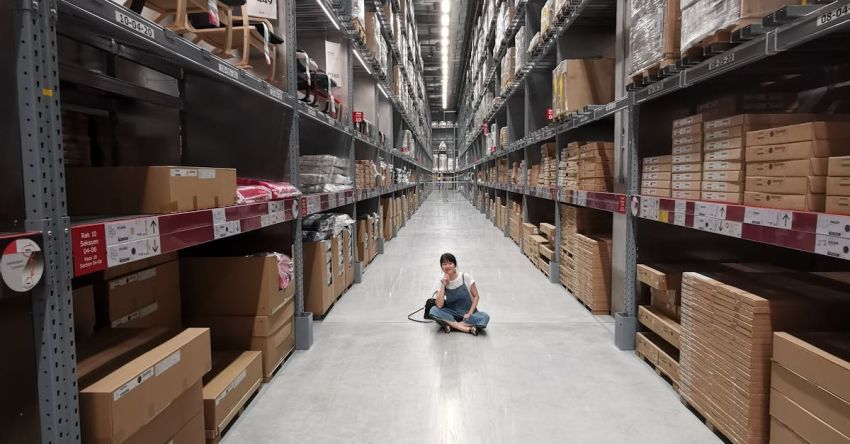
Efficient Inventory Management is Key to Success
For any business, managing inventory effectively is crucial to maintaining a smooth operation and maximizing profits. Poor inventory management can lead to excess stock, stockouts, and ultimately impact the overall performance of the business. By implementing best practices for inventory management, businesses can streamline their operations, reduce costs, and improve customer satisfaction. In this article, we will explore some of the best practices for inventory management that businesses can adopt to enhance their efficiency and profitability.
Utilize Inventory Management Software
One of the most effective ways to improve inventory management is by leveraging inventory management software. These tools provide businesses with real-time visibility into their inventory levels, allowing them to track stock levels, monitor sales trends, and optimize reorder points. Inventory management software can also automate tasks such as order processing, replenishment, and forecasting, saving businesses time and reducing the likelihood of human error. By investing in the right inventory management software, businesses can gain greater control over their inventory and make more informed decisions.
Implement Just-in-Time Inventory
Just-in-time (JIT) inventory is a strategy that involves keeping inventory levels as low as possible while still meeting customer demand. By adopting a JIT approach, businesses can reduce carrying costs, minimize storage space requirements, and improve cash flow. JIT inventory also helps businesses respond quickly to changes in demand and market conditions, making their operations more agile and efficient. However, implementing JIT inventory requires careful planning and coordination with suppliers to ensure that inventory is replenished promptly when needed.
Use ABC Analysis
ABC analysis is a method of categorizing inventory based on its value and importance to the business. By classifying inventory into categories A, B, and C based on criteria such as sales volume or profit margin, businesses can prioritize their inventory management efforts and allocate resources more effectively. Category A items are typically high-value products that contribute significantly to the business’s revenue, while category C items are lower-value products with lower demand. By focusing on managing category A items more closely and optimizing their inventory levels, businesses can improve their overall profitability and customer service.
Optimize Inventory Forecasting
Accurate inventory forecasting is essential for ensuring that businesses have the right amount of stock on hand to meet customer demand without overstocking. By analyzing historical sales data, market trends, and other relevant factors, businesses can predict future demand more accurately and adjust their inventory levels accordingly. Implementing advanced forecasting techniques such as trend analysis, seasonality modeling, and predictive analytics can help businesses anticipate changes in demand and make more informed decisions about inventory replenishment. By optimizing inventory forecasting, businesses can reduce stockouts, minimize excess inventory, and improve overall efficiency.
Establish Standard Operating Procedures
Establishing standard operating procedures (SOPs) for inventory management is critical for ensuring consistency and efficiency in day-to-day operations. SOPs outline the steps and guidelines for key inventory management processes such as receiving, storing, picking, and shipping inventory. By documenting and standardizing these procedures, businesses can reduce errors, improve communication among team members, and streamline their operations. Regularly reviewing and updating SOPs based on feedback and performance metrics can help businesses identify areas for improvement and implement best practices more effectively.
Monitor Key Performance Indicators
Monitoring key performance indicators (KPIs) related to inventory management is essential for evaluating the effectiveness of current practices and identifying opportunities for improvement. KPIs such as inventory turnover ratio, fill rate, stockout rate, and carrying costs provide valuable insights into the performance of the inventory management system. By tracking these KPIs regularly and comparing them against industry benchmarks or historical data, businesses can identify trends, pinpoint areas of inefficiency, and make data-driven decisions to optimize their inventory management processes. Regularly reviewing KPIs can help businesses stay agile and responsive to changes in the market and maintain a competitive edge.
Conclusion:
Effective inventory management is a cornerstone of a successful business operation. By implementing best practices such as utilizing inventory management software, adopting a just-in-time inventory approach, using ABC analysis, optimizing inventory forecasting, establishing SOPs, and monitoring KPIs, businesses can enhance their efficiency, reduce costs, and improve customer satisfaction. Investing in inventory management practices can lead to better decision-making, streamlined operations, and ultimately, increased profitability. By continuously evaluating and refining their inventory management processes, businesses can stay ahead of the competition and achieve long-term success.